While the world watches the next wave of Biotech innovation unfold, the infrastructure supporting it is quietly being tested in ways we’ve never seen before.
Global tariffs are disrupting supply chains. Skilled trades are in short supply. And the systems that power labs—air handling, water filtration, backup power, containment—are becoming more expensive and harder to maintain.
Resilience in a lab setting isn’t about backup plans. It’s about infrastructure that can absorb volatility—whether that’s a delayed part stuck in customs, a vendor short on cleanroom techs, or a sudden shift in how much budget is available for operations.
Challenge 1: Venture Capital Volatility and Budget Compression
Biotech venture capital has grown increasingly volatile since the pandemic-era boom. In 2024 alone, investors pulled more capital out of the sector than they put in for 42 out of 52 weeks (Cassel Salpeter, 2025).
That volatility doesn’t just affect funding rounds. It trickles down into capital projects, vendor relationships, staffing models, and day-to-day operations. Facility teams must stretch already-thin budgets while supporting highly regulated, high-stakes environments. As a result, facilities are postponing equipment replacements and lengthening maintenance cycles. And expectations for uptime, compliance, and environmental control haven’t budged.
This isn’t just a financial correction; it's an operational one. When investor sentiment cools, facility resilience becomes even more critical. You can’t rely on budget flexibility or just-in-time upgrades. You need systems that can absorb shocks, staff who can flex between roles, and visibility into every asset that can’t afford to fail. Facilities strategy isn’t just a support function anymore. In a volatile market, it’s a competitive advantage.
Challenge 2: Tariff-Driven Material Cost Volatility
Trade tensions are no longer a macroeconomic talking point; they’re a direct operational threat. The latest round of U.S. tariffs affects hundreds of imported goods, including many essential to lab and research operations and building infrastructure.
What’s at Risk:
- Imported lab infrastructure components like HEPA filters, fume hoods, biosafety cabinets, cleanroom flooring, and power management systems
Critical replacement parts for HVAC, lighting, and water purification systems sourced from Germany, China, and Japan
- Consumables such as lighting ballasts, air filters, or batteries that are usually low-cost but now show high volatility in price and availability
Impact on Lab Operations:
- Increased downtime waiting for parts that used to be “off the shelf”
- Unexpected spikes in repair or replacement costs
- Delayed capital improvement projects due to budget unpredictability
A recent Reuters report on Thermo Fisher Scientific noted that demand for lab tools and services remains strong, even amid global supply disruptions and tariff pressures. For facilities teams, this translates to sustained procurement delays and pricing volatility, especially for imported parts and specialized equipment. The challenge isn't just rising costs, but the uncertainty and cascading delays those costs can trigger.
Challenge 3: Labor Instability in Lab-Focused Facility Services
At the same time, labs are dealing with reduced budgets and labor shortages, and the skilled labor force that supports lab environments is thinning out. The labor crisis is no longer limited to front-line service roles. Now, it’s reaching into the trades and specialties required for Life Sciences.
The reality:
- HVAC technicians, cleanroom specialists, and certified GMP service providers are in short supply
- Wages are rising to compete, and so are vendor rates
- Turnover is climbing, especially in urban science hubs where demand far exceeds labor pool availability
Impact on Lab Operations: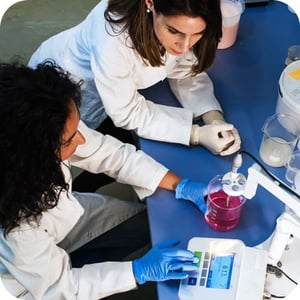
- Delays in routine maintenance, which, in a lab, can disrupt operations or compromise compliance and destroy research integrity
- Vendor instability that makes long-term planning difficult and increases the risk of service gaps
- Budget erosion as labor costs escalate faster than annual operating increases
According to IFMA, 45% of employers reported difficulties in finding the skills they need, with the figure rising to 67% among large organizations. Skilled trades, engineers, and technicians are among the top five in-demand roles, highlighting the growing challenge in sourcing qualified personnel for facility operations. In Biotech, where environmental tolerances are tight and downtime isn’t an option, these shortages become strategic risks.
Where does this leave Labs?
If you’re managing Biotech spaces, whether you’re on the client side or part of the property management team, you’re now operating in a market where:
- Materials are getting harder to find
- Labor is getting harder to source
- Budgets are increasingly out of sync with actual need
The result? Maintenance delays, supply shortages, increased materials cost, and equipment lifecycles cut short. Operational uncertainty is creeping into environments where precision and compliance are non-negotiable.
The Bottom Line
You can’t control tariffs. You can’t manufacture skilled tradespeople. But you can recognize the pressures that are building and begin to adapt before they reach a breaking point and halt science.
In Part 2, we’ll outline actionable strategies to help lab facility teams reduce their exposure, stabilize costs, and protect research continuity, even as external volatility continues.
Resilient lab operations start with a clear understanding of your facility’s vulnerabilities. Flagship Lab Services offers a Science Ready Assessment (SRA)—a comprehensive review of the critical systems, staffing, and workflows that keep your lab compliant, operational, and ready for anything.
Learn more about the Science Ready Assessment and see how Flagship Lab Services can help your lab stay ahead of volatility.
Leave a Comment