In every scientific endeavor, the precision of equipment plays a pivotal role. Calibration maintains this precision by aligning instruments to trusted standards. But like all processes, it's not immune to errors.
By understanding and minimizing these errors, you can ensure the integrity of your measurements and the credibility of your findings. This blog post aims to shed light on some of the most common calibration errors and provides insights on how to mitigate your risk.
The Important Role of Calibration in the Lab
Calibration – the process of comparing the measurements or readings of a scientific instrument to a known and traceable standard – is key to ensuring the accuracy, precision, and reliability of your equipment output. This is achieved by adjusting the instrument to provide measurements consistent with established reference points.
Not only does calibration reduce the risk of costly errors, but it prevents unnecessary downtime due to malfunctioning equipment. There are many other benefits to regularly calibrating your equipment, including:
- Increases efficiency
- Improves safety
- Ensures compliance
- Strengthens reputation
Common Calibration Errors
Careful calibration lays the foundation for accurate measurements and successful research. But, even if you follow best practices, errors can sometimes occur. Here are some of the most prevalent calibration errors and their implications.
Zero Calibration Error
Zero calibration error, often referred to as "zero error," is among the most common errors observed in measuring instruments. This error occurs when the instrument does not read zero when the true value of the measured quantity is zero. This means that even when there is no input (i.e., no weight on a scale or no pressure in a pressure gauge), the instrument does not display a zero reading.
There are two types of zero errors:
- Positive Zero Error: When the instrument reads a value greater than the actual zero.
- Negative Zero Error: When the instrument reads a value less than the actual zero.
It's essential to recognize and correct zero error because it can introduce a constant offset to all measurements made with the instrument.
Span Calibration Error
This error occurs during span calibration – the process of ensuring that the instrument correctly reads the known standard at the high-end value. If the instrument doesn't read the known standard correctly during span calibration, the difference between the instrument's reading and the true value of the standard is the span calibration error.
When you combine zero and span calibration errors, you get an error that widens as you continue using the instrument. Correcting both errors ensures that the instrument provides accurate readings throughout its entire measurement range.
Linearity Calibration Error
Linearity calibration error refers to the deviation of an instrument's readings from a straight-line reference over its entire operational range. Ideally, an instrument should have a direct proportional relationship between its input and output across its full range.
This error causes the equipment's response to assume an irregular line. As such, it does not relate to span or zero calibration errors, which assume a straight line.
Hysteresis Calibration Error
Hysteresis calibration error refers to the difference in an instrument's output readings for a given input, depending on whether the input value is approached from a lower value (increasing) or a higher value (decreasing). This type of error is a manifestation of the instrument's memory of its previous state and its inability to return to the same position for a given input when approached from two different directions. One way to identify this error is to perform an up-down calibration test.
How to Minimize Calibration Errors
Calibration errors in instruments can arise from a variety of sources – including everything from temperature fluctuations to human mistakes. Understanding and accounting for these factors can help minimize calibration errors.
Calibrate in Ambient Conditions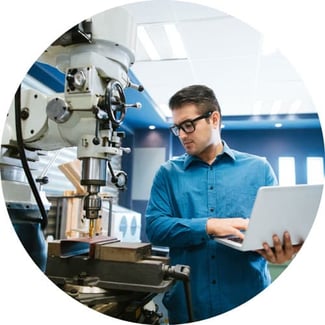
Calibrating instruments in ambient conditions is crucial because many instruments are sensitive to environmental variables such as temperature, humidity, and atmospheric pressure. By calibrating in conditions that closely mirror the typical usage environment, you can increase the likelihood of consistent operations. If calibrated in non-ambient conditions, the instrument might exhibit discrepancies when used in its standard environment due to the effects of environmental factors.
Calibrate at Regular Intervals
Over time, wear and tear, environmental factors, and other influences can cause instruments to drift from their calibrated state. Regular calibration detects such deviations, enabling you to correct issues in a timely manner. Not only should you calibrate equipment at its recommended interval, but you should calibrate after critical measuring projects and other major events.
Trust the Calibration Experts
Equipment experts possess the knowledge and experience needed to handle sophisticated equipment, understand the nuances of calibration procedures, and can accurately interpret results. Improper calibration, often a result of untrained handling, can lead to systematic errors and compromise the integrity of your data. Additionally, trained professionals are aware of potential pitfalls and can take preventive measures, ensuring not only the precision of the instrument but also its longevity and optimal performance.
Flagship Lab Services is a leading provider of laboratory equipment services, including calibration, validation, and maintenance.
With a commitment to quality and innovation, we offer a range of equipment solutions to support your research, development, and production needs.
For more information about our comprehensive lab support services, visit our lab services page.
Leave a Comment