In today’s complex economic landscape, trade tensions and global supply chain issues dominate the headlines. From tariffs on imported goods to geopolitical disruptions, there’s no shortage of concern about how these global events might impact facility management budgets. But while material costs may spike here and there, they’re not the true culprits behind most of the cost pressures facing facility teams today.
Imported equipment and supplies may become more expensive, but they make up just a small percentage of your facility operations budget. In most cases, the real cost pressure comes from a source you already manage every day – your people. And unless you address labor strategically, no amount of tariff avoidance will stop your costs from rising.
The Immediate Impact of Tariffs (and Why It’s Limited)
Both the in-force and pending tariffs will raise the price of select materials and specialized equipment, especially those imported from China. For some facilities, they may affect upgrade timelines, supply contracts, or one-off projects.
But for most day-to-day operations, tariffs have a more indirect effect. Most facility budgets are not material-heavy; they are labor-intensive. The cleaning crew, the HVAC tech, the facilities supervisor, the team performing preventive maintenance or responding to tenant requests – That’s where the real money goes. And those costs have been climbing for years, with no sign of slowing.
Labor: The Silent Cost Engine
On average, 60 to 80 percent of a facility’s operating cost is tied to labor for salaries, benefits, and management. That means even minor increases in wages, benefits, and turnover rates have a greater impact than major changes in materials pricing.
Why is this cost driver so often overlooked? Unlike material costs, which can spike visibly and draw media attention, labor increases tend to be more subtle:
- In annual renewals with baked-in escalators
- In compliance updates that require new training
- In quiet turnover that leads to hiring gaps and inefficiencies
Key Factors Driving Labor Costs
Here’s a closer look at what drives labor costs up, regardless of what’s happening in global trade:
- Rising Minimum Wages and Local Mandates: New regulations across major cities and states continue to push base rates higher, often above national averages.
- Aging Workforce and Skills Gap: Skilled trades professionals are retiring faster than they’re being replaced. The talent pipeline is thinning, and wages are rising to compete.
- Complex Union Negotiations: Contracts are becoming more layered, with cost-of-living adjustments and benefits expectations that escalate year over year.
- Soaring Benefits and Insurance Costs: Health coverage, liability insurance, and workers ' comp costs continue to rise. These are costs that employers must absorb or pass through.
Increased Compliance Demands: Heightened standards for safety, background checks, onboarding protocols, and documentation add time, cost, and risk to hiring and retention.
Each of these alone may seem manageable. Together, they put sustained upward pressure on facility maintenance budgets.
How tariffs and labor interact
The oversized impact of labor on facility maintenance budgets doesn’t mean tariffs don’t matter.
If capital projects get delayed due to trade-related costs, that can lead to deferred maintenance. If the budget is reallocated to offset material price increases, that may result in a freeze on hiring or longer hiring cycles.
The two forces are intertwined, but it’s labor that’s constant, compounding, and closer to your control.
Coming Next: Strategies to Take Control of Your Labor Costs
You can’t stop inflation. You can’t avoid market volatility.
But you can re-engineer how labor is structured, sourced, and managed across your facilities.
In Part 2, we’ll share the smart strategies leading facility teams are using right now to reduce labor costs without cutting corners, from predictive staffing models and preventive maintenance to vendor consolidation and performance-based hiring.
Don’t Wait: Assess Your Labor Risk Now
The best time to assess your labor structure was six months ago. The second-best time is today.
Flagship offers facility assessments that go beyond surface-level reviews to uncover hidden labor inefficiencies, staffing gaps, and cost-escalation points so you can make a course correction before your budget takes another hit.
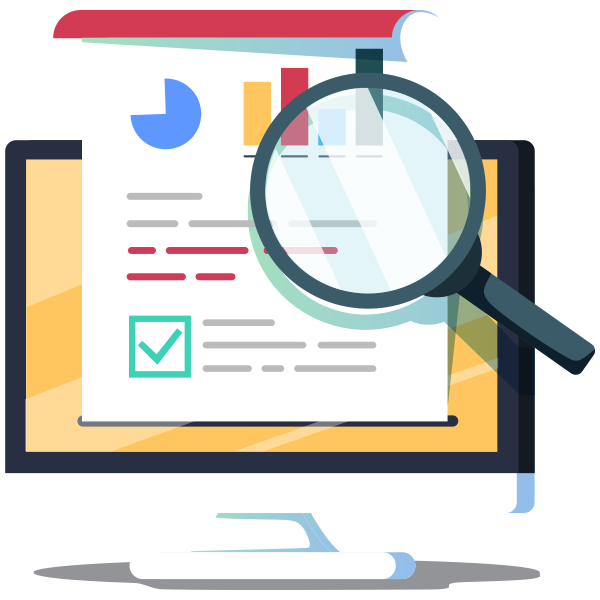
Do you want to claim your complimentary facilities assessment?
Reach Out Now
Leave a Comment