In Part 1, we exposed the often-overlooked truth about facility costs: Tariffs may draw media attention, but labor costs are what drives your bottom line. With labor accounting for up to 80% of a facility’s operational spend, any cost control effort that doesn’t start there is missing the point.
Fortunately, you don’t need to wait for market conditions to improve. You can act right now.
Five Proven Labor Strategies Facility Leaders are Using Today
These aren't reactive band-aids. They're proactive, scalable strategies that create long-term resilience.
- Right-sizing labor with data
Stop staffing based on outdated templates and square footage alone. Today’s FM leaders optimize staffing by using occupancy data, usage patterns, time-of-day analytics, and task frequency trends. The result: the right team, at the right time, doing the right work.
- Cross-training for flexibility
Labor shortages make siloed teams a liability. Cross-training employees to flex across multiple roles, cleaning, light maintenance, grounds, and client-facing tasks helps reduce downtime, improves job satisfaction, and lowers overall headcount needs.
- Retaining talent through better culture and onboarding
High turnover is one of the costliest and most preventable challenges in facilities. Strong onboarding, mentorship, recognition, and upward mobility not only reduce replacement costs but also enhance service quality. Partnering with an FM provider who invests in retention pays dividends.
- Consolidating vendors for efficiency
Multiple vendors often mean duplicated supervision, inconsistent quality, and unclear accountability. Smart leaders are moving toward integrated FM partnerships where one provider handles multiple service lines under a single management structure, simplifying operations and reducing admin overhead.
- Shifting to preventive maintenance models
When facilities are forced into reactive mode, labor costs spike. Proactive, scheduled maintenance lowers urgent requests, reduces overtime, extends asset life, and smooths out staffing demand. It’s a win on every level, but it requires strong CMMS tools and partner discipline.
How the right partner can help you get ahead of labor costs
It can be a challenge to find a facilities services partner that employs all five strategies. Flagship Facility Services supports clients’ cost containment goals with:
- Centralized recruiting teams that reduce fill times and ensure staffing consistency across locations
- Cross-training programs to build agile, multi-capable teams
- Centralized scheduling and data visibility for smarter labor deployment
- Preventive maintenance systems that reduce reactive labor
- A retention-first culture that keeps skilled employees in place, reducing costly turnover
Labor is a cost you can control
If you’re still focused on tariffs, you’re reacting.
If you’re focused on labor, you’re planning.
Let us help you assess your current labor model, from staffing to supervision to retention, and uncover hidden costs, gaps, and opportunities to save.
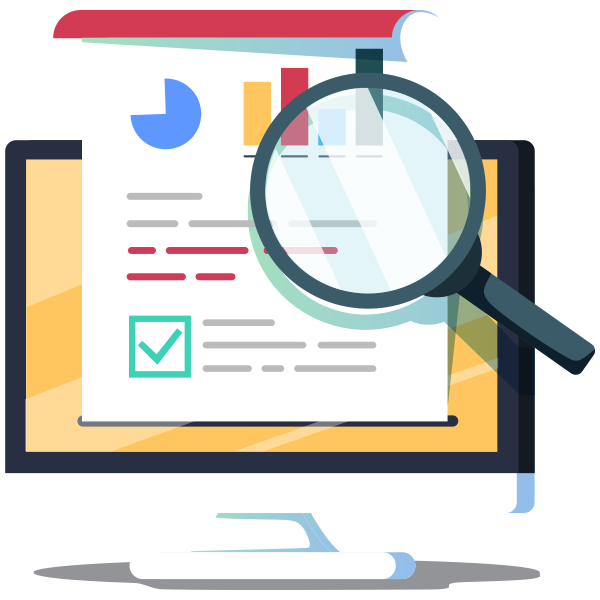
Do you want to claim your complimentary facilities assessment?
Reach Out Now
Leave a Comment